Machine Guarding Hazards

Moving
machine parts have the potential to cause severe workplace injuries.
Any machine part, function, or process that may cause injury must be
safeguarded.
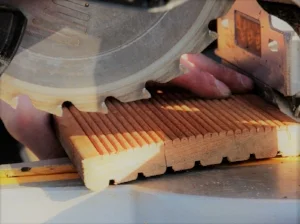
Industrial
workplaces such as garage workshops, metal fabrication and welding
shops, and mechanical or heavy manufacturing facilities will have a
variety of machines and tools. Some of the tools may be as simple as a
table saw or box fan and sometimes they can be complex and partially
robotic and involve hazardous chemicals. Workers responsible to operate,
repair, clean, or just work near these machines and tools must be
protected from potential hazards.
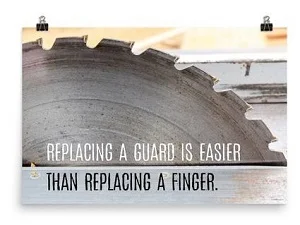
Machine
guards are critical to the safety of workers. Many times, workers do
not realize the dangers that they are protected from because of a simple
steel or acrylic guard. For this reason, workers should be familiar
with the potential hazards introduced when machines with rotating parts,
gears, or pulleys are used.

OSHA Standard 1910.212(a)(1) Types
of guarding. One or more methods of machine guarding shall be provided
to protect the operator and other employees in the machine area from
hazards such as those created by point of operation, ingoing nip points,
rotating parts, flying chips and sparks.
Recognizing
the potential hazards of machines starts with understanding the first
place where the potential for injury exists – this is the “point of
operation.” According to OSHA the point of operation is the area on a machine where work is actually performed upon the material being processed. Workers have to be protected from point of operation hazards.
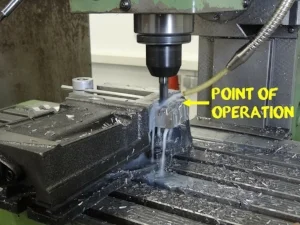
OSHA Standard 1910.212(a)(3)(i) Point of operation is the area on a machine where work is actually performed upon the material being processed.
Workers
have to be protected from point of operation hazards, power
transmission apparatus such as pulleys and chains, and other moving or
rotating parts that pose danger to the operator. Workers should be
familiar with the potential hazards introduced when machines with
rotating parts, gears, or pulleys are used.
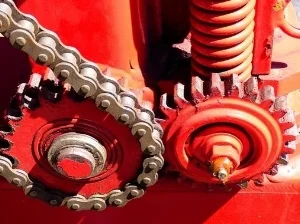
OSHA Standard 1910.212(a)(3)(ii) The
point of operation of machines whose operation exposes an employee to
injury, shall be guarded. The guarding… shall be so designed and
constructed as to prevent the operator from having any part of his body in the danger zone during the operating cycle.
There
are a variety of ways that workers could be protected from machine and
point-of-operation hazards – some techniques require special training in
order to ensure the safety of the operator.
Fixed Guards
– made of acrylic, metal, or even plastic that are bolted, welded, or
locked in place provide stable protection from moving parts.
Adjustable Guards
– self-adjusting or manually adjustable guards that allow the material
to be of multiple sizes or shapes but still protect the worker.
Interlocked or Sensors
– sometimes combined with adjustable or removable guards, interlocks or
sensors can be set to instantly shut off power to a machine. Sensors
may be designed to shut off a machine or tool as soon as a visible or
invisible barrier is broken.
Safety Trip Controls
– similar to interlocks or sensors these devices can be in the form of
metal bars, steel cables or wires, and floor mats or gates that are
designed to trip and shut off power to a machine if a worker touches,
steps, or enters a danger area.
Restraints and Pullbacks
– devices such as wrist straps and safety ropes attached to specific
points to keep the worker from getting too close to a point of operation
hazard.
Comments
Post a Comment